Electric motors are a lot lighter than engines that run on jet fuel but add the batteries and you quickly wind up with a design that is heavier per mile flown than any other option. The problem for today’s designers is that those other options could still be years away. And it is not for want of trying.
Last month at the Farnborough International Airshow, Airbus and Boeing signed development and financing deals with startups working on jet fuels that would get them closer to net-zero targets. Boeing’s deal with UK startup Firefly and venture-capital fund Clearsky is intended to provide it with a biofuel cooked from waste sewage.
“We spent some time identifying a suitable feedstock for sustainable aviation fuel that was abundant and everywhere in the world, which led us to sewage biosolids,” said Firefly CEO James Hygate.
Though it emits carbon dioxide into the upper atmosphere, government agencies consider fuel from agriculture and waste to be clean. And it does at least work in today’s jets. But aircraft makers’ big hope for the future is hydrogen as it avoids carbon entirely though it means an overhaul of aircraft design.
“If we can scale up hydrogen, it becomes really exciting. In my view, hydrogen is a game-changing fuel for aviation,” argued JoeBin Bevirt, CEO of aircraft startup Joby Aviation, in a panel session at the show. “The specific energy of hydrogen is three times higher than that of [conventional] jet fuel.”
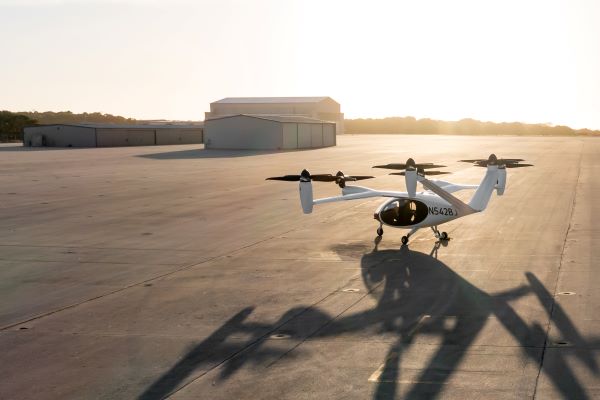
But as a bulky gas that slowly degrades metal tanks and pipes in its natural form and a liquid form that needs cryogenic cooling, hydrogen is a long way from becoming the primary fuel for even small, lightweight aircraft. The primary fuel source for most of Joby’s designs so far, on its way to building a commercial, vertical takeoff “air taxi”, are lithium-ion battery cells not all that different from those used in SUV-grade electric cars.
Battery power
Twenty years ago, Pipistrel flew a battery-powered plane that could stay in the air longer than ten minutes. Focusing on the market for training, where the aircraft only needs to carry a couple of people and no cargo on relatively short hops, the Slovenian company carved out a niche for itself based on lower maintenance costs. Over the past couple of decades, a growing band of startups have been trying to push up range and capacity to a point where battery power becomes viable not just for air taxis but the “thin haul” market. This covers the many tiny airfields and strips dotted around most countries and across chains of islands. Some companies, such as Canadian seaplane operator Harbour Air, are retrofitting their vehicles for all-electric flight. Others are turning to brand new designs. Last year, Scandinavian Airlines started taking bookings for flights expected to take place in 2028 on Eviation’s battery-powered, 11-seater Alice.
Above: Eviation's Alice achieves milestone with first all-electric flight
Though estimated range has dropped from 650 nautical miles when first announced in 2018 to closer to 250, partly to satisfy safety margins for distance and weight, airlines see this as viable for a model where flight patterns move from the traditional hub-and-spoke model to one where people fly in small numbers point to point.
Joby sees routes of less than 30 miles being most common for its five-seater air taxi. But with a relatively mature battery, Bevirt claims the vehicle can fly routes of several hundred miles.
“We chose the air taxi because we thought that it’s the best way to get going with today’s batteries. We’ve done 450 miles, so we can fly lots of hops and we don’t necessarily have to recharge after every flight.”Having bought a hydrogen-propulsion specialist a couple of years ago, parallel work is going into aircraft that combine batteries and the gas. “We converted a battery aircraft to hydrogen-electric. The fuel cell functions as a range extender so we could take our aircraft and fly it 520 miles.”
Hybrid flight
For longer-distances and higher capacity, hybrid flight may become the most common option. One option is to reduce development risk and opt for not-quite-net-zero operation.
French startup Voltaero uses an internal combustion engine derived from one of Kawasaki’s motorcycle designs in its Cassio. This drives the rear propeller for an extra boost to the two forward, electrically driven propellers and can also recharge batteries mid-flight. One less-explored option is to reserve the conventional aviation fuel for safety reserves that all aircraft need, providing power through a generator instead of going through a gearbox to a propeller. This would cut emissions to a minimum but still provide the power needed for go-arounds or diversions to a landing site hundreds of miles away.
The net result is a lot more electrification throughout the aircraft. But uncertainty surrounds even that. Engineers have discovered more problems of operating high-power electrical systems in high-altitude flight, not least because some projects are looking to push craft well above the cruise limit for commercial jets to exploit lower levels of friction. As designers look to increase capacity, the amount of power that electric motors can provide has come under scrutiny in recent years, with research projects pushing specific power from a relatively easily attained 10kW/kg to 20kW/kg or more. That leads to more complex motors and drive electronics, though wide-bandgap semiconductors look to be capable enough to support the transition.
The University of Nottingham, which has a 200-strong team working on various aspects of electrified aviation, has designed a modular drive unit for 12-phase motors that will go into a prototype hydrogen powertrain.
To get increased power to the motor efficiently, voltages need to increase beyond the 250V or so used in conventional aircraft. The larger the aircraft, the more it makes sense to increase the voltage of the distribution cabling and circuitry to save weight. Projections for future long-haul aircraft that swap out traditional engines for motors see the bus voltage climbing as high as 5kV.
The Nottingham design, in common with other prototype small aircraft, works with an 800V supply bus. Ideally, voltages would go higher. But associate professor Tao Yang points that one important reason for sticking at 800V in the short term lies in the ready availability of power devices rated to 1.2kV. In a two-level design, there is enough headroom in terms of breakdown voltage. Manufacturers may switch to three-level multiphase converters if they can deal with the cooling problems and miniaturisation when these circuits are integrated into the motors themselves to save on weight and size.
There are big issues with high-voltage power conversion that come with high altitude. One is the Paschen curve, which describes how insulation breakdown voltage follows air pressure. At cruising altitude, it can drop to a little over half its value at sea level. That leads not just to a higher risk of arcs but partial discharges that gradually wear away at insulation.
Avoiding partial discharges means paying greater attention to insulation and conductor density. And it may mean bringing in new insulation materials for cables as voltages increase. Yang points out cosmic rays as another source of risk. The high-energy spikes can lead to sudden voltage surges that exceed the breakdown voltage of power transistors.
There is a lot that could derail these plans when you consider how the fuel and power issues will be combined with the high levels of autonomy that startups such as Wisk Aero and Joby reckon they would need for airlines to operate a huge fleet of air taxis. Manuel Heredia Ortiz, managing director of Crisalion Mobility, another runner in the air-taxi race, warned in his keynote at last month’s airshow a consolidation seems inevitable considering the number of players working on smaller aircraft. But in the meantime, the pace of development signifies a renewal of excitement over technology in the aviation sector.
“That got lost in the past 20 years. We lost people to finance and the internet. But that’s changing now. We’re making aviation great again.”