Working with models: the key qualities designers need in a platform for virtual design
4 mins read
Automotive systems are starting to approach the same level of software complexity that modern operating systems contain – anything up to 300million lines of code. In fact, these systems are even more complex, since interaction with the vehicle's mechatronic system is far more important: cars can kill you; computers probably won't.
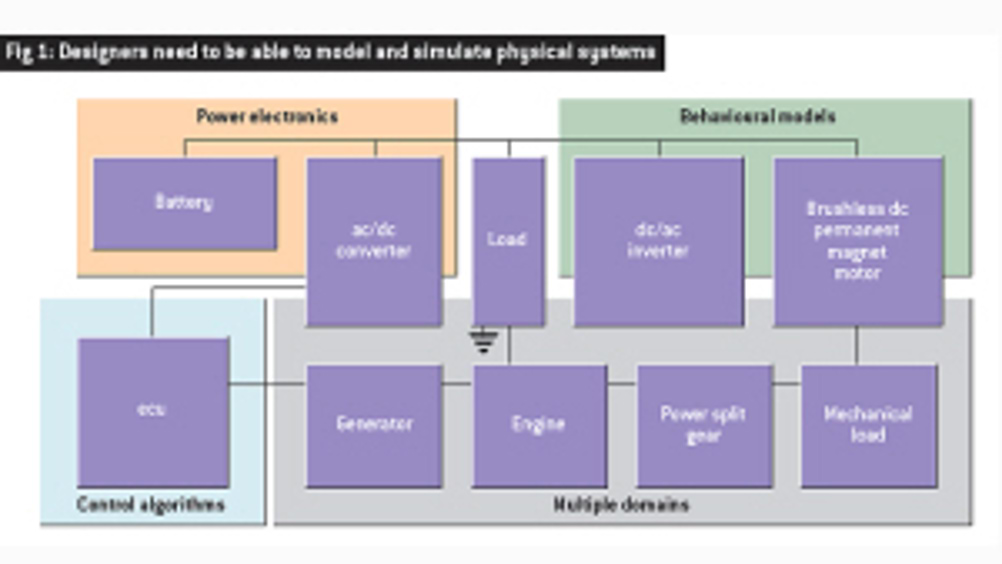
The cost of electronics has increased to 60% of the car for electric hybrids. The cost is not in software, but in the electronic, electrical and electromechanical components that make up the vehicle.
At the 2010 SAE International conference, top automotive engineers took part in a panel session, during which they identified the main system design challenges. These were: function and software allocation and verification; system engineering and simulation; and power generation, management and distribution.
We look at these three challenges in more detail below.
Function and software allocation and verification
The key challenge for automotive systems engineers is that software makes the problem harder. Making cars that don't crash, that serve up driver information without distraction and that don't pollute are among the greatest challenges the industry faces. On top of that, success depends on there being sufficient demand for cars, which means design teams are constantly under pressure to find the latest 'cool factor'.
The essence of system design is to create a distributed computing system that interacts with physical systems and then define and map software onto this distributed system. This task was more straightforward when every electronic control unit (ECU) in the vehicle mapped to a single function and the ECU/software was delivered as a black box: an approach that means it's now common to find more than 100 ECUs in high end vehicles.
To reduce this number, technology now exists to consolidate multiple functions into one ECU. However, complexity has also increased such that multiple ECUs must cooperate to implement a high level function. Tasks like automatic parking or collision avoidance must communicate with and control multiple subsystems. A big challenge in integrating systems is that components invariably come from multiple suppliers. This compromises safety and quality: at the start of ECU software integration, there may be thousands of errors.
System engineering and simulation
How can automotive design teams conquer the challenges that come with vehicle electrification? The problem scope is not limited to software and electronics – design teams must also consider mechatronics. Potential solutions need to support detailed physical modelling, conceptual design and implementation, and concurrent, multiple tiers of modelling and verification.
Carmakers need models for multiple purposes: for analysing/verifying the product need; to define software applications of the EE system; and to support simulation and verification of the plant/multiphysics/car system models.
Consequently, modelling requires the use of different frameworks:
• AUTOSAR – software running on a virtual processor
• EAST-ADL2 – software running in an environment
• VHDL-AMS/MAST – mechatronics modelling and electrical systems,
• SystemC/SystemC-AMS – system level description of SoCs and their interconnection
• SystemVerilog/Verilog-AMS – SoC implementation
• SPICE – analogue design.
Bringing these elements together requires a platform capable of modelling and simulating physical systems, which enables full system virtual prototyping for applications in analogue/power electronics and electric power generation, conversion distribution and mechatronics (see fig 1). To be useful, a platform must incorporate an electrical system architecture that links semiconductors, software and mechatronics.
Power generation, management and distribution
The vehicle's core function is still the generation, management and consumption of electricity. This is more pronounced with electrification, since the power train is now a factor in all of these areas. All electrical systems need to make use of low power techniques so electricity consumption can be reduced and, with it, battery size.
Electrical load can be reduced by optimising 12/24/48V loads, by reducing the amount of wire in the vehicle and by designing more efficient heating, ventilation and air conditioning systems.
Compared to automotive, sectors like the mobile phone industry have more experience of applying low power techniques. Here, battery life plays a large part in determining the success of mobile software platforms. In turn, software has a large part to play in determining battery life. For example, an application that wakes up the phone every 10 minutes for just 8s to perform updates can cut its stand by time by half. Any software power inefficiency or malfunction can quickly cause a drop of 5x or more in standby time.
Debugging power defects comes with another major issue. In low power modes such as 'suspend', the embedded debug service is also likely to be suspended. In addition, any debug interaction is intrusive and tampers the power figures. Furthermore, expensive lab equipment is required to perform a sufficiently fine granular power profiling to determine which of the components is the most critical.
In many ways, the challenges that designers face – whether they're working on mobile phones or electric vehicles – are converging.
Automotive engineering solutions
Synopsys' design automation solutions help to address emerging automotive engineering challenges. It has solutions for the design of silicon, it can provide solutions for virtual platform verification of software and it can partner with the leading solutions for software creation. Synopsys also offers Saber – a leading tool for mechatronics design – and leads the creation of the standard languages used, including MAST and VHDL-AMS.
• Virtual solutions
Virtual prototypes help vehicle designers to overcome function and software allocation and verification challenges. They provide debug visibility at the right level of abstraction, such as OS process traces, and can be instrumented with information that characterises power usage.
Their execution is controlled via deterministic scenario scripts that drive the I/O of the virtual prototypes, such as generating user input via a touchscreen controller, setting GPS coordinates through a UART or initiating a phone call. During simulation, power analysis data is collected, alongside other hardware and software traces, to enable root cause analysis and debugging that allows engineers to optimise the software.
Increasingly, automotive design teams are shifting to a virtual approach to manage the growth in system complexity (see fig 2). A virtual prototype provides a fast, fully functional software model of the interacting subsystems, executing unmodified production code and providing higher debugging analysis efficiency.
• System engineering
All systems are subject to variation, including component tolerances, environmental stresses and ageing. Automotive engineers want to reduce the effects of variability on system performance by designing systems that are less sensitive to variation. Saber helps engineers to apply robust design methods, such as Taguchi or Design For Six Sigma and to optimise their mechatronic systems for quality and cost.
• Power management
The links from Saber to transistor level cad tools enable engineering teams to speed product design for power electronic systems. By abstracting device level physics to physical systems, designers can work with accurate, compact Saber models of power components. The abstracted models support behavioural circuit simulation that can be hundreds of thousands of times faster than device level mixed mode simulation.
David Smith is a Synopsys scientist, responsible for the architecture of the Saber product lines.